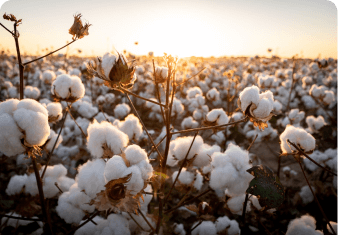
01
TRUST & TRANSPARENCY FROM THE START
Partnerships with regenerative, organic, recycled and transitioning cotton farmers supply Saitex Mill with raw materials.
COTTON
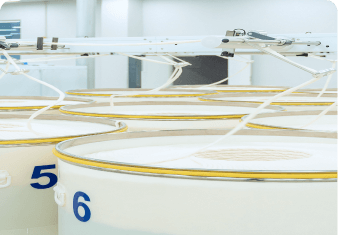
02
FROM WHOLE COTTON TO HIGH-QUALITY YARN
Spinning capabilities allow blending of different materials using dual-core, multiple-core, and SiroSPUN™ technology.
SPINNING

03
MORE EFFICIENCY LESS LEFTOVER
Weaving machines use high-efficiency rapier looms, creating the best quality woven fabrics.
WEAVING
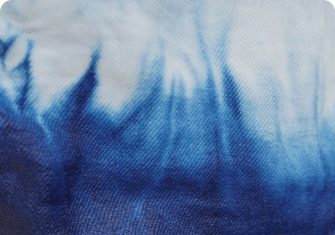
04
Smart-Indigo™ DYEING RESPONSIBLY AT SCALE
Our Smart-Indigo™ system utilizes an electrochemical-dye bath preparation that emits 90% less CO2, consumes 70% less energy, and 30% less water where the only waste product is oxygen. Finishing mechanisms, also using the latest technology, include singeing, mercerizing, pad-batch dyeing, pad-steam dyeing, stentering, sanforizing, and fabric tumbling.
DYEING / FINISHING
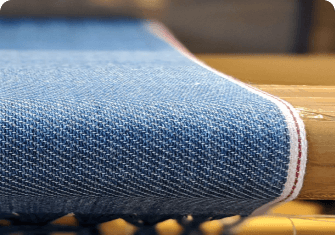
05
24 MILLIONS OF FABRIC PER YEAR
The mill’s machinery uses less energy, fewer chemicals, and less water creating the most environment-friendly processes with capabilities to produce 24 million meters of fabric per year.
FABRIC
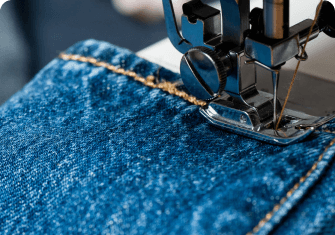
06
18,000 GARMENT PER DAYS
Our RFID Data collection system provides us real-time production data to take instant decisions during the production process. Allowing us to maximize our productivity while reducing our extra fabric needs from the traditional 5% to 1% only.
CUTTING & SEWING
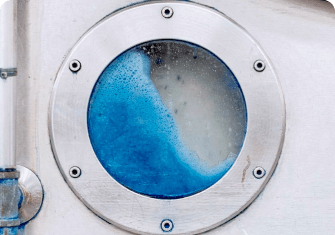
07
98% RECYCLED WATER + 2% EVAPORATED = ZERO DISCHARGE
Thanks to our closed-water system, each year we are able to save 430 million liters of water – equal to the annual water consumption of 432,000 people.
LAUNDRY / FINISHING
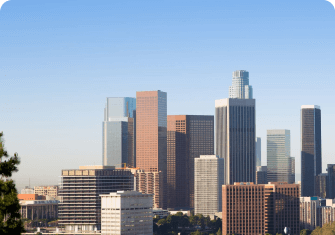
08
THINK GLOBAL, ACT LOCAL
Support the local economy by expanding our activities to the United States, with a semi-automated manufacturing.
USA FACTORY
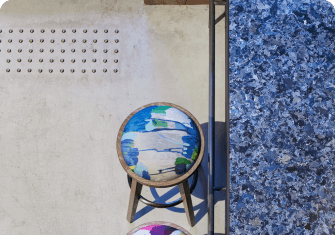
09
ELIMINATE THE WORLD EXCESS, ONE STITCH AT A TIME
We are embracing circularity to tackle textile waste by giving a new life to the garment offcuts and dead stock. Made of discarded garments, STELAPOP turns waste into valuable products. Allowing us to save trees and climate landfills for a regenerated future.
UPCYCLING

10
COLLABORATIONS
There is no sustainability without social justice. Rekut was born with the intention to do better for our communities, by providing equal pay and opportunities to people with different abilities.
REKUT
Contact
Do better, together.
We are always looking for like-minded partners to join our mission and change the way things are done.
CONTACT US
LA, USA
Dong Nai, VN